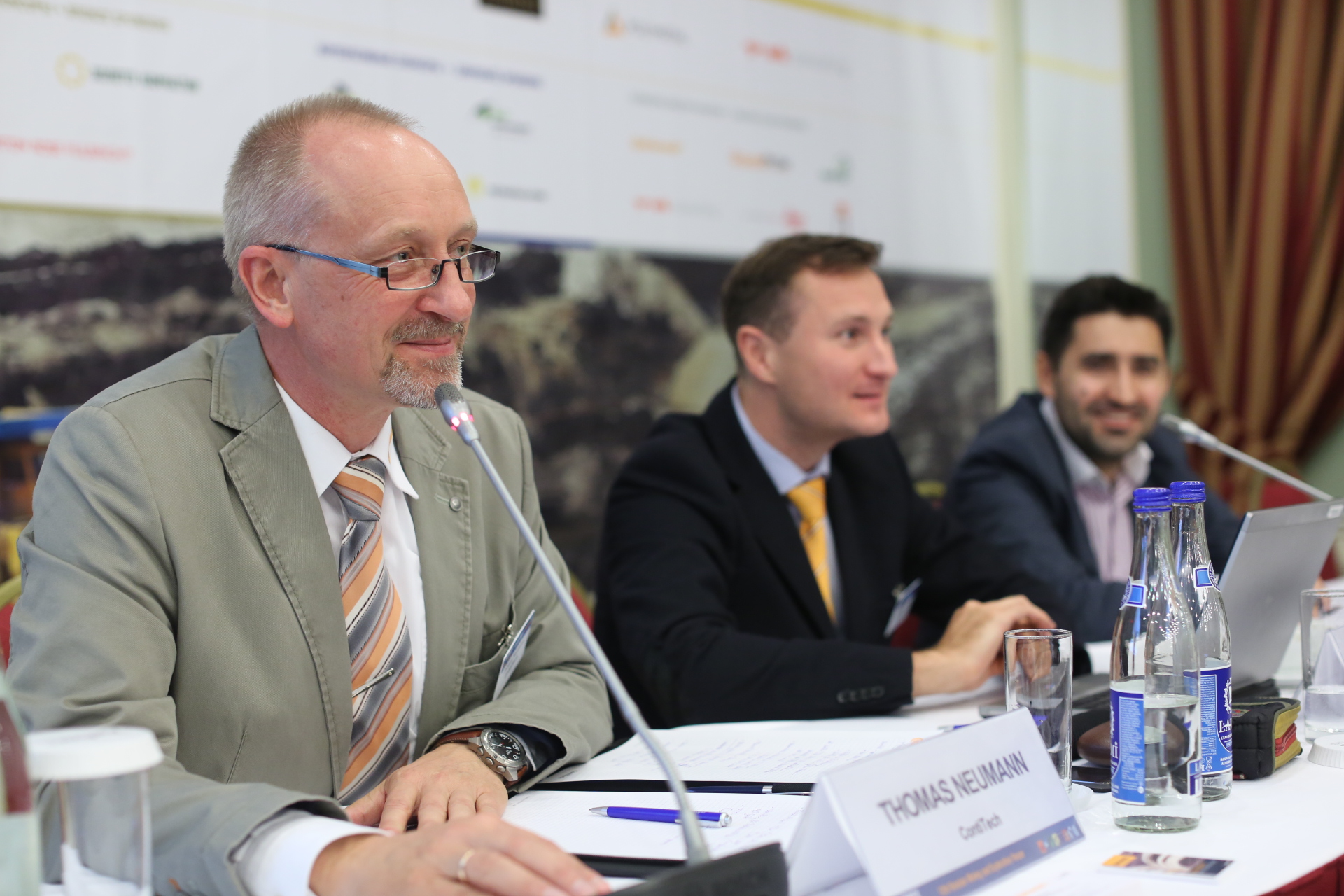
Мастер-класс-посвященный технологии крутонаклонных и вертикальных конвейеров почти полностью состоял из сессии вопросов и ответов, конкретизирующих реалии работы этого вида транспорта. По мнению организаторов – компании ContiTeck, – главным было показывать удачные примеры его использования.
Томас Нойманн представил решения по крутонаклонным и вертикальным конвейерам. На примере уранового рудника он показал, что транспортные расходы могут достигать 43% от общих расходов. «Принцип такой: транспортные расходы составляют большую часть расходов».
В настоящее время руда перевозится, главным образом, грузовиками. Чтобы сравнить расходы на конвейер и колесный транспорт, представители компании взяли железорудный карьер с производительностью 3 млн тонн в год, сырьем определенной плотности и расходами на топливо 15 евро за литр и маршрут 5 км. Сравнивались экскаватор+5 грузовиков + транспортная служба и экскаватор + два самосвала + конвейер. Экономия составила 75 млн руб. в год.
Второй пример был рассчитан в Германии 1990-е годы прошлого века. Расчеты показали, что при производстве 0,5 млн тонн руды в год и высотой подъема 100 м экономия составит 43% или 20 млн руб. в год.
При принятии решений оказывается, что у недропользователей нет доверия к конвейерному транспорту. Тем не менее, господин Нойманн привел примеры по использованию конвейеров. Так, в Болгарии работает рудник производственной мощностью 3 тыс. тонн в час, уклон его составляет 15%. Второй пример – трубчатый конвейер длиной 4.3 км диаметром 7,5 тыс. мм, который отвозил золу с ГРЭС. Еще один пример из России – «Северсталь», которая использует на руднике Айкон технологию сэндвич-конвейера (один над другим), транспортируя 1,5 тыс. тонн руды в час, подъем составляет 127 метров, угол наклона –36 градусов.
Последний пример – конвейер, где руда не просто транспортируется, а дополнительно проходит химическую обработку, становясь тем самым частью технологической цепочки завода.
Ирина Швец из «Северстали» спросила, учитывались ли затраты на дробление в карьере и делается ли для конвейера дополнительное дробление. Томас Нойманн признал, что расходы не дробление не учитываются, а его коллега Андрей Минькин объяснил, что сейчас трубчатые конвейеры диаметром 900 мм позволяют перевозить руду уже после первичного дробления с кусками диаметром до 35 мм. Последние исследования показали, что для крупнокусковой руды возможен уклон до 45%.
Другой участник мастер класса поинтересовался, как влияет на специфику проектирования карьера то, что для транспортировки будет использоваться конвейер. Оказалось, что крутонаклонный конвейер может наращиваться в длину по мере углубления карьера, но перемещение его связано с большими издержками. Конвейеры позволяют снизить количество самосвалов, но не как устройство, которое полностью заменит грузовики. Отвечая на уточняющий вопрос, представители ContiTeck отметили, что в смешанных системах на долю конвейерного транспорта приходится около 30% общей производительности карьера. Ирина Швец из «Северстали» напомнила, что и коэффициент использования конвейеров невелик: на узбекском руднике Мурунтау он составляет лишь 36%. Внятно возразить или прокомментировать эту цифру представители организаторов мастер-класса не смогли.
Большинство сэндвичных конвейеров в мире имеют высоту до ста метров. Но есть и исключения: например, на том же Мурунтау руда транспортируется на высоту 270 м. Если говорить о подземной отработке, можно сэкономить на диаметре скипа: традиционно он составляет 7-9 м, тогда как для вертикального конвейера по технологии pocket lift достаточно диаметра 2-3 м. В существующих скипах оставшееся пространство можно использовать для подъема тяжелых грузов. Кроме того, можно сэкономить на энергопотреблении, которое снижается в 4-6 раз. В этой части участники заинтересовались, можно ли использовать pocket lift для абразивных руд (к которым не относятся гипс и уголь). Оказалось, что АЛРОСА использует эту технологию на своих ОФ при транспортировке абразивного кимберлита. Кроме того, в Турции используется вертикальный конвейер для транспортировки медной руды.
Представитель «Полиметалла» спросил о минимальной мощности рудника для использования конвейеров и попросил сопоставить капзатраты для колесного и конвейерного транспорта. Представитель ContiTeck признал, что конвейер для рудника мощностью 350 тыс. тонн в год (около 30-50 тонн в час) – «это какой-то очень маленький конвейер», но позже признали, что для золотой руды это может быть оправдано. В целом существующая тенденция, напротив, – необходимость увеличение мощности конвейера до 10 тыс. тонн в час, рост наклона до 45-50% и использования руды первичного дробления. Ирина Швец попыталась представить, как разбирать заштыбовку, если сойдутся крупные куски руды, а кран использовать невозможно. Андрей Минькин признал, что действительно для конвейера самое страшное – это так называемые «рыбы» или «лещи» – длинные куски руды, которые ложатся поперек ленты. Для этого предусматривается специальный режим заполнения.
Александр Дамали из таганрогского «Промтяжмаша» поинтересовался, что делать, если транспортируется липкая руда на ленте вертикального конвейера. Решение для таких руд – использование встряхивателей, работающих от энергии движения ленты без собственного привода.
Еще один вопрос касался сопоставления железнодорожного и конвейерного транспорта. Томас Нойманн признал, что такие расчеты не проводились, но предположил, что капзатраты на установку железнодорожной ветки могли бы быть примерно на 20-30% выше, чем на колесный транспорт. Но Андрей Минькин привел пример, когда железнодорожная транспортировка была заменена на конвейерную. Первый пример – отгрузка золы на предприятии в Болгарии после того, как его приобрела американская AES. Второй пример – угольная шахта в Юте. Конвейер работает уже 20 лет. Илья Копухин из «Северстали» подтвердил, что при выборе между железной дорогой и конвейером компании выбирают конвейеры (если только расстояние не измеряется сотнями километров). Но если железнодорожный транспорт уже есть, обычно от него не отказываются. И заверил Томаса Нойманна, что конвейер на Олконе исправно работает.
Выступление Ильи Копухина вызвало интерес у «Полюса Золото», который попросил назвать реальный КТГ (коэффициент технической готовности), достигнутый на данный момент. Тот припомнил, что показатель «точно был больше 90%». «Там используется двухступенчатое дробление – и первичное, и вторичное дробление осуществляется в карьере, и потом по конвейеру диаметром 80 см поднимается наверх», – пояснил Томас Нойманн.