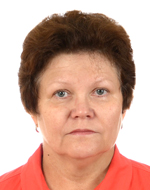
In 1980 graduated from the Irkutsk National Research Technical University, Metallurgical faculty, with a specialisation in physicochemical methods of metallurgical processes research. Since 1979 has been working at the Irkutsk Research Institute of Precious and Rare Metals and Diamonds, Irgiredmet, as a laboratory assistant, an engineer, a junior researcher, a researcher, a senior researcher. From 2006 to the present day holds a position of leading researcher at the hydrometallurgical laboratory. In 1999 defended candidate's thesis “Research and development of technology for precious metals recovery from flotation concentrates using activated carbons”.
Development of recovery technology for complex gold-bearing ores.
Over the last years, the Irgiredmet Institute has performed a significant amount of studies on complex gold-bearing ore processing. Selection of recovery technology for complex gold-bearing ores is defined by material composition, ore grade, recovery rate using different process flowsheets. The report presents the results of development of gold and other precious metals recovery technology from gold-bearing ores, iron gold ores and gold-antimony ores. Gold-bearing ore refers to the gold-quartz low-sulphide ore type. Copper is a main contaminant during gold recovery from ore using cyanidation, which results in high reagent consumption (sodium cyanide and calcium hypochlorite). The technology of gravity-flotation processing with intensive cyanidation of gravity concentrates and CIL gold recovery from a mixture of intensive cyanidation cakes and flotation concentrates is presented. Reagent costs and consumption can be reduced using the technology of wet CIL tailings conditioning using recirculating cyanide solutions. The tests showed that this approach allowed to decrease sodium cyanide consumption from 17 to 11 kg per 1 ton of concentrate, and obtain copper in the form of high-quality concentrate. Iron gold ore refers to the sulphide magnetite gold ore type. Valuable components of the ore are gold, iron and bismuth. The technology of flotation processing of ore with sorption cyanidation of flotation concentrates, magnetic separation of flotation tailings with producing magnetic concentrate, and flotation of bismuth from CIL tailings with producing a saleable bismuth concentrate was developed. Also, the technology of in-situ hydrometallurgical production of bismuth was worked out. Gold-antimony ore refers to the gold-bearing quartz-antimony ore type. The developed technology of gravity-flotation processing allows to obtain Dore gold (produced as a result of primary gold concentrate smelting) as a saleable product and a marketable gold-antimony concentrate. Hydrometallurgical methods of gold recovery from concentrates were studied. Gold-antimony concentrates are characterized by low gold recovery rate and high reagent consumption. The most promising technology is thiocarbamide leaching of concentrates, which provides selective gold dissolution, whilst hydrometallurgical processing tailings represent a saleable antimony concentrate, which can be further processed for antimony recovery with hydrometallurgical or pyrometallurgical methods. Plant design standard operating procedures have been issued for the given objects.